Wear Plates - How to Cut Wear Plates?
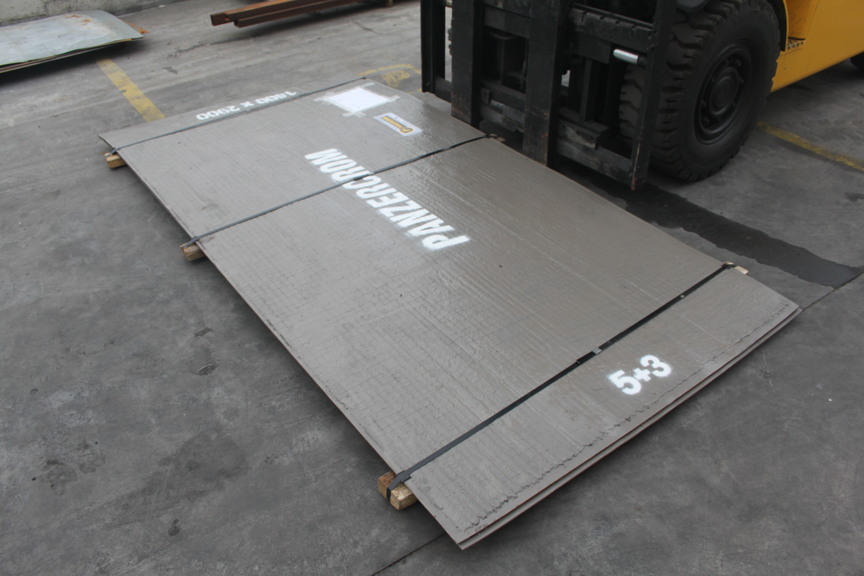
How to Cut Wear Plates?
Wear plates can not be cut with oxy-acetylene or oxy-propane methods due to high carbide content.These plates must be cut with plasma or laser cutting method. CNC controlled machines are used for cutting as seen from the image below for multiple or complex pieces.
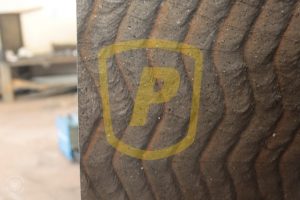
Manual plasma cutting machines are preferred for low quantity and partial cuts.
Things to consider during the cutting process:
During cutting, the hardfaced surface must be on the top. Otherwise, an accurate cut might not be possible since cutting flame will contact with hardfacing alloy after penetrating to St37 (S235).
If the hardfaced side placed as a bottom side, base material St37 (S235) will fuse and explode and this will provide unsuccessful surface cut on hardfaced side. As a result of this unsuccessful application, an angled cut surface might be achieved rather than linear cut surface.As a result of this wrong method, long and laborious grinding is needed to fix the cut surface.
If manual cutting using plasma is required, it's important to follow specific procedures to ensure safety and accuracy. The cutting process should begin from the hardfaced surface side, and the cutting arc must initiate from the edge. However, if the plasma machine's cutting power is insufficient, starting the arc directly on the hardfaced surface can lead to arc kickback and potential damage to the plasma nozzle, electrode, and torch head.
To prevent this, a safer method involves drilling a hole into the material using a cutting electrode first. Once the hole is created, the cutting arc should be started at the edge of the hole. The cutting process can then proceed by pulling the torch inside along the diameter. This approach ensures both a secure and precise cut while minimizing the risk of damaging the plasma equipment.
It's worth noting that while cutting electrodes, carbon electrodes, and spiral grinding can be utilized for cutting, they are not the most suitable methods in most cases. Spiral grinding, for instance, could potentially damage the hardfaced surface during cutting. Additionally, when using a grinding machine, caution is needed to avoid getting hewn stone lodged between the base material (St37/S235) and the hardfacing. This situation could lead to an explosion and serious injuries.
For effective wear solutions, including wear plates and welding consumables, you can explore Panzercrom® offerings. Further information about their products can be found on their website: https://www.panzercrom.com/en/panzercrom-plate-wear-plates/. Panzercrom® specializes in serving various industries, such as the cement and concrete industry: https://www.panzercrom.com/en/cement-and-concrete-industry/.
If the cutting power of the preferred plasma machine is insufficient and if arc is started directly on hardfaced surface, arc can kickback and plasma nozzle, electrode and torch head might be damaged.When cutting process is done with manual plasma, instead of using plasma arc directly on the surface, a hole must be drilled with a cutting electrode first and the piece must be cut by starting the arc at the edge of the hole and cutting along the diameter by pulling inside. Thus, both safe and accurate cut is obtained and the risk of damage for plasma equipment is minimized.Other than mandatory situations, although cutting electrode, carbon electrode and spiral grinding can be used for cutting, theoretically, these are not correct approaches. Especially, during cutting with spiral grinding, hardfaced surface might be damaged.After completing some part of the cutting process, the grinding machine must not be tucked in. Hewn stone might stuck between base materialSt37 (S235) and hardfacing, explode and cause serious injuries.
Discover Panzercrom® wear plates; https://www.panzercrom.com/en/panzercrom-plate-wear-plates/
Discover our focus industries; https://www.panzercrom.com/en/cement-and-concrete-industry/
You can contact us from https://www.panzercrom.com/en/contact/ for more information about our wear solutions, wear plates and welding consumables.
Follow us on social media;
Linkedin: https://www.linkedin.com/company/panzercrom
Instagram: https://www.instagram.com/panzercrom/
Facebook : https://www.facebook.com/panzercrom/