Wear Plates – Types of Mounting and Tips
.jpg)
Wear Plates – Types of Mounting
In wear plate mountings, bolt systems might be necessary for fastening - fixing instead of welded connection due to construction requirements. When creating the project, you have to consider that wear plates are composite materials and they act differently from regular base materials. After defining the hardness of wear plate, different bolting, countersinking, tapping, stud welding etc. methods can be applied to wear plate. Companies that have not experience with wear plates might have unsuccessful results when they try joining welding applications on hardfacing sections. These improper joining welds might lead to cracks, fractures and ruptures under impacts, compressive and tensile loads.
Bolt - Sleeve - Tapping Processes:
Bolt - sleeve - tapping processes on the wear plate may cause additional costs. Some constructions might need thousands of these applications. If a company does not have sufficient experience, they might disregard this situation. If this process is necessary due to construction: Necessary amount of holes must be drilled on the wear plate to prepare for the next process.
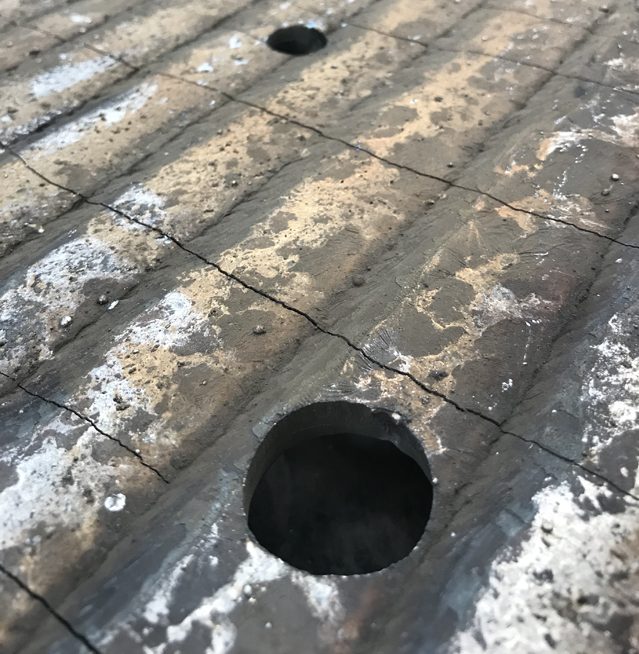
Colleting - twisting is needed. Depending on bolt type and property, ring - twisting is necessary on the lathe; if there will be tipping, rings must be processed if countersunk or flat bolts will be used. Top and bottom part of the ring must be manufactured with a chamfer for healthier welding process at the next stage. Rings must be placed in pre-prepared holes on the wear plate. Then, after welding with a basic-type electrode on the backside (St37/S235 base material side), ring circumference must be welded circularly with high elongation properties welding consumables (ex. welding electrode with Ni alloy) on the hardfaced side. If regular welding consumables are used while welding, region that contacts with hardfacing will crack due to high tension.
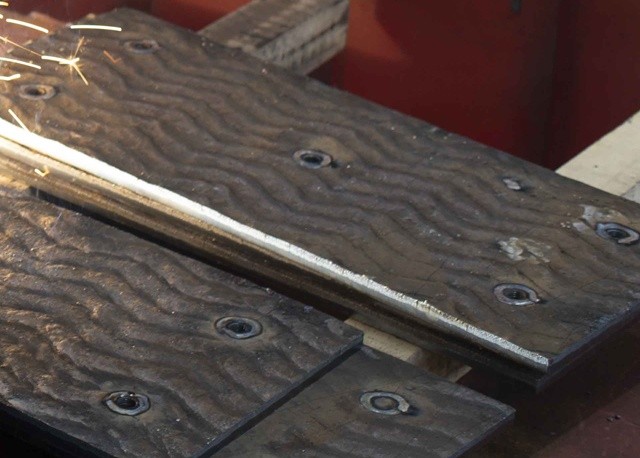
After all these processes are completed, preventive hardfacing must be applied on the surface of the joint welding for avoiding possible wear on joining weld metal.
Stud - Bolt Welding Application:
If studs are needed due to construction (studs are generally required on the back surface with St37/S235 base material), these studs must be welded with a basic electrode. If high mechanic properties are expected, medium or high-alloyed welding consumable materials with high mechanic properties must be used instead of basic electrodes. In bolt application, the bolt is welded to the bottom part of St37/S235 base material (non-welded side) and basic electrodes will be sufficient. Due to construction, if the bolt is required on the hardfaced surface, a hole must be drilled to embed the bolt inside and high mechanical properties welding consumables must be used on the hardfaced side and also on the non-welded side.
Discover Panzercrom® wear plates; https://www.panzercrom.com/en/panzercrom-plate-wear-plates/
Discover our focus industries; https://www.panzercrom.com/en/cement-and-concrete-industry/
You can contact us from https://www.panzercrom.com/en/contact/ for more information about our wear solutions, wear plates and welding consumables.
Follow us on social media;
Linkedin: https://www.linkedin.com/company/panzercrom
Instagram: https://www.instagram.com/panzercrom/
Facebook : https://www.facebook.com/panzercrom/